The path to climate neutral passenger transport at Munich Airport
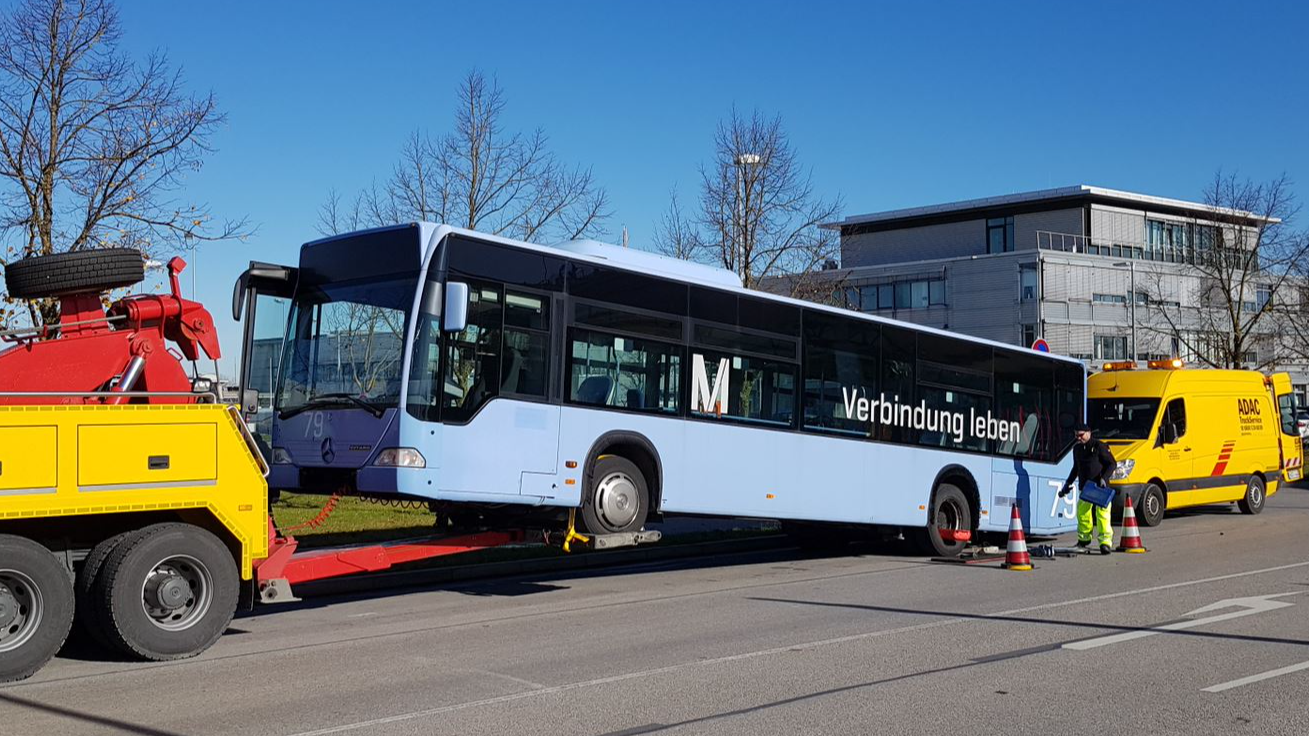
The Challenge
The Munich Airport has committed to become CO2 neutral until 2030. It currently operates 53 buses to transport passengers from the gates to the airplanes. The buses are responsible for emissions of around 2,000 tonnes of carbon dioxide per year.
Shifting this fleet to solely battery electric vehicles is difficult, because it would lead to significant stress on the existing electric power supply network. Approximately 2MW electrical power would be needed during 8 hours in the night for charging the buses. The buses are often used for up to 16 hours a day, covering about 150 to 200 kilometres, which is comparable to city buses. Routes can be difficult to plan ahead due to constant, albeit often minor, shifts in flight operations.
On the other hand, the apron buses have a particularly high demand for air-conditioning energy, especially in winter, due to the long door opening times. Heating via heat pumps or even electric heating significantly reduces the range of battery-electric vehicles.
Fleet operators like the Munich Airport need a solution for their buses, which enables the heavy vehicles to..
... run on zero emission renewable energy.
... not stress the local electricity grid.
... operate 16 hours per day.
... fulfill changing routes and timetables.
... provide enough energy for heating or cooling of the passenger compartment.
The Solution
The solution consists of upcycling a used Mercedes Citaro 1 with the CMF drive. The chassis gets a new powertrain, which saves both costs and 90 tons of carbon dioxide emissions.
The key characteristics of the solution are:
- Independence of the electric supply network,
- Efficiency of the CMF drive,
- Long range and operating hours
- regional and CO2 neutral fuel (bio-LNG)
The CMF drive is a battery-electric powertrain with an on board charging station. Recuperation is possible. Also, the gas engine is deployed in its optimal working point which means that part load losses are avoided. Compared to a conventional Diesel engine it operates up to 30% more efficient at the Munich Airport.
The range of the current configuration is approximately 800km, which is about 3-4 times more than a battery-electric bus of similar size. Unlike battery-electric buses this range does not get significantly reduced during winter, because the heat output of the onboard charging station is used for maintaining the temperature set point in the vehicle.
Bio-LNG is made from biological wastes and residues. The production of bio-LNG from CM Fluids absorbs more carbon dioxide than the well-to-wheel process chain emits
The key to this effect is the methane concentration of biogas. Biogas consists mainly of methane and carbon dioxide in equal parts. To separate these two components, the gas gets liquified. In other words, producing a certain amount of methane also means absorbing an equal amount of carbon dioxide.
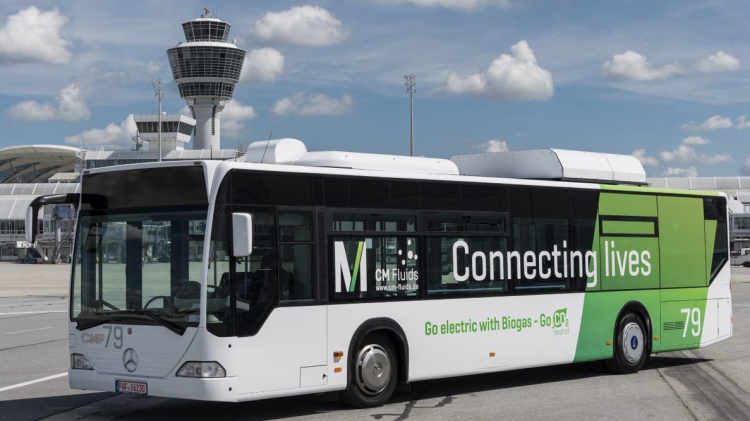
Making an impact
The technology is more economical and environmental-friendly than other alternative mobility solutions. The absolute environmental impact of one bus might be small, but it is the first step for applying this technology on more buses. Each upcycled bus saves about 800 tons of CO2 equivalents over a lifetime of 12 years.
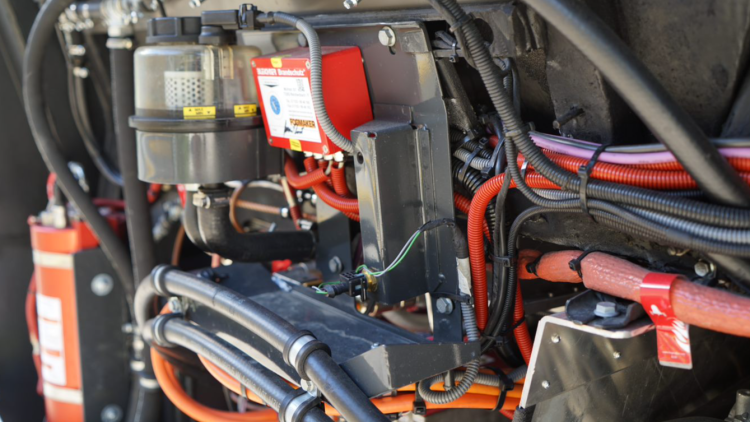
Lessons learnt
- The CMF drive is able to solve the task of making commercial vehicles like buses orf trucks climate neutral. Especially for vehicles with long operating hours and frequent starts and stops
- Unless the up-cycling of buses like in this project saves lot of resources many customers prefer new buses. CM Fluids therefore started cooperating with established bus manufacturers to be able to provide new buses with the CMF drive.